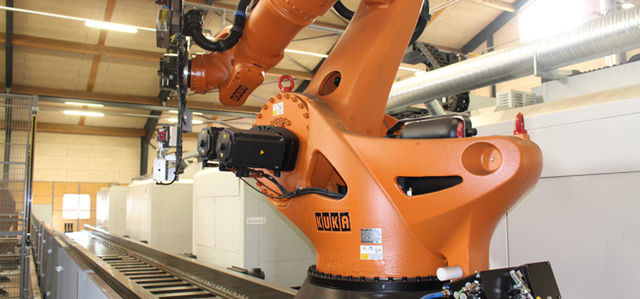
Installasjonen har gått raskt og det har vært kjørt emner gjennom hele tiden
Bransjens største robot hos Multicut
Den største Kuka-installasjonen i Danmark, og samtidig bransjens største robot, står hos Multicut A/S i Vildbjerg, der den støtter et FMS-anlegg med fire CNC-sentre for bearbeiding av store og tunge emner.
På de seks første månedene har den store Kuka-roboten hos Multicut allerede flyttet drøyt 10 000 tonn inn og rundt i bearbeidingscellene – og ut igjen.
«Det er utvilsomt den største roboten vi har hatt med å gjøre, en riktig kraftkar som alltid står klar til å flytte emnene inn og ut av arbeidsstasjonene», sier QRS’ tekniske sjef Hans Jørgen Gam, som har stått for robotdelen ved Multicuts FMS-celle.
På den siste stasjonen, rett før emnene forlater FMS-anlegget, finnes det en annen, mindre Kuka-robot som freser og avgrader hullkantene, slik at de blir helt glatte og er klare for bruk. Frese- og avgradingsroboten benytter Kukas Force Torque Sensor-system, slik at operasjonen kan kompensere for emnenes temmelig store variasjoner.
Hans Jørgen Gam er godt kjent med virksomhetens robotbruk, ettersom han har vært ansvarlig for mange installasjoner ved maskinene i årenes løp. Alle robotene kommer fra Kuka og er oppstilt i umiddelbar tilknytning til Mazak-maskiner.
«Det store anlegget, som omfatter fire Vision Wide V-Tec-maskiner som Multicut selv har kjøpt inn fra produsenten i Taiwan, er en løsning for håndtering og sluttbearbeiding av store, tunge emner. Det finnes flere varianter, så vi har også skapt forskjellige fiksturer, i tillegg til at robotens gripere er tilpasset de forskjellige emnestørrelsene», forteller Hans Jørgen Gam.
For QRS er det en ekte turnkey-løsning, der man i samarbeid med Multicut har funnet frem til de ønskede spesifikasjonene for så å spesifisere en løsning som oppfyller kravene. Det har pågått et intenst arbeid i hallen siden man begynte å stille opp utstyret, og etter seks uker kunne man starte opp bearbeidingen i henhold til planen.
SIKKERHET I FOKUS
Installasjonen har gått raskt og det har vært kjørt emner gjennom hele tiden. Samtidig har FMS-cellen blitt optimert.
«Vi har fått den nesten helt ubemannede driften til å fungere under stort sett hele prosjektet. Enkelte ting har vi forbedret under arbeidets gang gjennom en løpende dialog med Multicut. Men i store trekk er den opprinnelige planen vi la sammen, også den som har blitt realisert», sier Hans Jørgen Gam.
Sikkerhet i produksjonen har vært en viktig faktor. Det er ingen vits i å bore flere hull hvis det samtidig betyr at risikoen for feil øker. Her er roboten en stor fordel:
«Det er viktig at arbeidsgangene stemmer, slik at roboten laster på ett sted samtidig med at de tre øvrige sentrene kjører. Da utnytter vi maskinkapasiteten maksimalt. Vi har dratt full nytte av Kuka-robotens styring, og kan stole på at emnet plasseres riktig før bearbeidingen og deretter etterkontrolleres når det tas ut igjen, sier Hans Jørgen Gam.
Når emnene er så store og ikke 100 prosent plane, slik tilfellet er her, skal det ikke så mye til for at hullet forskyves. Det har vi imidlertid tatt høyde for, slik at det bores nøyaktig der det skal bores.
Multicut har angitt hvor stor gjennomstrømning de ønsker, og så har Hans Jørgen Gam stort sett hatt frie hender til å gjennomføre det.
På sikkerhetssiden har Kuka og QRS bidratt med økt personsikkerhet gjennom Kuka Safe-Operation. Dette systemet består av en innebygd sikkerhets-PLC og en rekke lysgitre og sikkerhetsskannere, som sammen danner rammen for en sikker arbeidsplass. Kuka Safe-Operation er en sentral enhet som sikrer området og arbeidssonene, og styrer i tillegg en stor del av samarbeidet mellom de to robotene.
SYKLUSTIDER SOM PASSER
«Vi kunne godt ha kjørt raskere med robotene, men det kunne ha ført til ventetider, og også større risiko for feil. Vår oppstilling med 4 maskiner som arbeider to og to, gir ønsket output med maksimal prosessikkerhet, slik at feilemner kan unngås», sier Hans Jørgen Gam.
Det har vært utfordringer. For eksempel er det ikke bare å åpne en maskin og legge inn emnet:
«Vi jobber med virkelig store emner. Det er en utfordring for roboten å flytte disse inn og ut når det er begrenset med plass. Det har vi også funnet en løsning på. Den ekstra tiden det tar med de største emnene, henter vi inn gjennom raskere transportkjøring. På den måten er flyten fortsatt tilpasset fremstillingen av mindre emner i maskinene ved siden av, og den totale produksjonen optimal», forklarer Hans Jørgen Gam.
Avhengig av sluttkundens behov kan ønsket antall emner kjøres gjennom ved at de lastes inn satsvis. Både før og etter bearbeiding kan emnene plasseres i tilpassede stativ som sendes direkte til montasjeavdelingen.
«Iblant skal mindre størrelser produseres på alle fire maskinene samtidig, andre ganger produseres fire ulike emnestørrelser i maskinene uavhengig av hverandre. Dette avstemmes med behovet for hvilke størrelser som skal bearbeides. Vi har valgt å ha to store sentre og to litt mindre. På den måten kan vi kjøre de største emnene på de store, og de mindre på de to andre», sier Hans Jørgen Gam.
Dette er et bevisst valg av Multicut basert på forventningene til produksjonen.
KOMMER HELT TETT PÅ
For QRS generelt og Hans Jørgen Gam spesielt er det et privilegium å arbeide for Multicut:
«Vi kommer helt tett på de utfordringene som vår løsning skal brukes til. Den gjensidige tilliten vi har bygd opp betyr at vi også kan vise hva robotene kan, samtidig som vi får den nødvendige innsikten til å kunne foreslå de rette løsningene», sier Hans Jørgen Gam, og fortsetter:
«Multicut vet godt hva de vil ha, men de lytter også til oss når vi har ideer til hvordan vi kan oppnå det. Det gir et godt samarbeid som gjør at vi sammen får maksimalt ut av virksomhetens investeringer.»
Det mangeårige samarbeidet er et godt fundament og bidrar til gjensidig respekt og engasjement. Det gjør også at man får ut det lille ekstra som ellers er lett å overse ved den teoretiske planleggingen av et prosjekt.
Målsettingen om å flytte drøyt 10 000 tonn inn i FMS-anlegget og ut igjen som ferdige emner i løpet av de første seks månedene, er nådd. Løsningen er implementert, og Multicut er nå klar til å møte etterspørselen etter emnene.
Aggreko øker batteriinvesteringene til 200 millioner dollar for å støtte energiovergangen
Aggreko har økt sine globale investeringer i mobile batterilagringssystemer (BESS) til rundt 200 millioner dollar, slik at flere bedrifter kan få tilgang til den nyeste batteriteknologien og nå sine mål om netto nullutslipp.
Ny Emerson Flushing Ring
TESCOM AGI Flushing Ring fra Emerson med modulær montering for bruk ved skylling. Ved å gi en fullstendig og modulær ventilmontering med et enkelt delenummer effektiviserer skylleringen i AGI BR-serien bestilling og legger til rette for enkel bestilling på nytt med bestemte testkrav fra kunder. Både de tradisjonelle ringene i BRS «sandwich»- og BRW «wafer»-stil er tilgjengelig, samt BR7-designet i «integrert deksel», som omfatter lufting/skylling i selve flensringen.
Ny kraftig SCARA-robot fra KUKA
– raske bevegelser og 60 kg nyttelast. KUKA lanserer nok en SCARA-robot denne høsten. En kraftig modell med en maksimal nyttelast på 60 kilo. SCARA-roboter har flere fordeler. De er energieffektive, kostnadseffektive og kan bevege seg raskt med svært høy presisjon, sier Micael Amandusson, channel manager hos KUKA Nordic.
Neste generasjon PLS teknologi
Beckhoff muliggjør et reelt sprang i ytelse innen automasjonsteknologi med TwinCAT PLC++. Både utvikling og hastighet kan akselereres, samtidig som de velkjente fordelene med TwinCAT, som konsekvent integrasjon, kompatibilitet og åpenhet, fortsatt leveres.